長寿の半割れ型給電チップ
1. 半割れ型給電チップの開発(有限会社大幸エンジニアリングと共同開発)
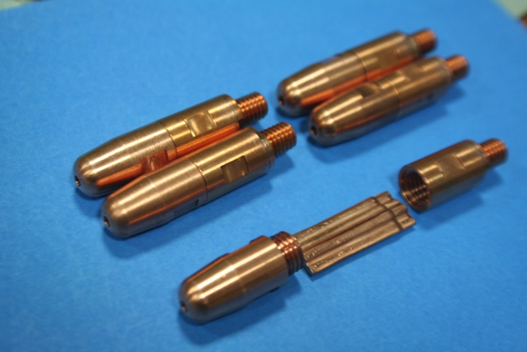
国内特許および中国特許取得
長寿半割れ型給電チップの技術資料はこちらをご参照ください。
2. 開発の背景
自動車産業では実ライン自動車産業では実ラインでのアーク溶接の主流はガスシールドのミグ(MIG)/マグ(MAG)溶接が主流となっており、ロボット溶接が多く採用されている。
ここ10数年間でアーク溶接電源の大きな進歩により、インバータ電源、デジタル電源と進歩し、スパッタの発生が著しく低減した。すなわち、フローニアス社のCMT溶接法、ダイヘンのシンクロフィードGMA溶接法、パナソニックのMTS-CO2溶接法およびSP-MAG溶接法、JFEEスチール社開発のJ-STAR溶接法などを採用することで、短絡時の発生スパッタを低減している。ガスシールドアーク溶接では用いるシールドの成分により毎分0.2g以下にすることもできる。溶接電源、溶接ワイヤおよびシールドガスなどの観点からスパッタの低減を図られてきた。
しかし、給電チップの開発についてはこの40年間に、革新的な大きな進歩はなかった。チップ形状も図1に示すような銅合金製の一体型のもので、構造の変化が少なく、一部コーティングを改良したものや、強制加圧給電型ノズルに用いるコレットチップがある程度である。ロボット溶接ではその寿命が2時間~8時間程度のものである。長時間溶接すると、図2に示すように、円形の穴が摩耗により楕円形に変形して、頻繁に取り換えをする必要がある。このようにチップの摩耗が進むと溶接ワイヤの狙い位置が大きくズレ、溶接欠陥を生むことになる。1.2mm径のワイヤに対して、穴の径が、約0.2mmとか0.3mmの拡大があった場合に、チップの交換を余儀なくされる。
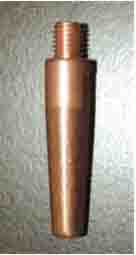
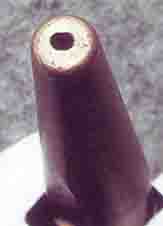
図1 従来型チップ 図2 穴形状の摩耗状況
そこで弊社では、まず、給電チップの摩耗現象を考察した。クロム銅が高温の鋼ワイヤと接触したときの引っ掻き摩耗現象である。その時の摩擦力、銅の温度、引っ掻き速度、銅の硬さなどが影響するが、この中でも銅の温度に注目した。すなわち、図3に示すように従来の一体型チップではパックワイヤなどのようにワイヤ癖のひねりがあると、チップ内部で給電し、その給電点がひねりとともに変動する。図3の左図のようにチップ中央で給電が起こったとすると、この点とワイヤ先端との間に次式に示すようなジュール発熱がワイヤ内部に発生し、鋼ワイヤの温度が約800℃以上にもなる。
また、給電点の変動は真のワイヤ突出し長さを変動させる。すなわち、図3の右図の場合には突出し長さが短くなり、溶接電流が増大し、左図の場合には突出し長さが長くなり、溶接電流が低下する。アークが長くなったり、短くなったりして、アークの安定性が損なわれる。
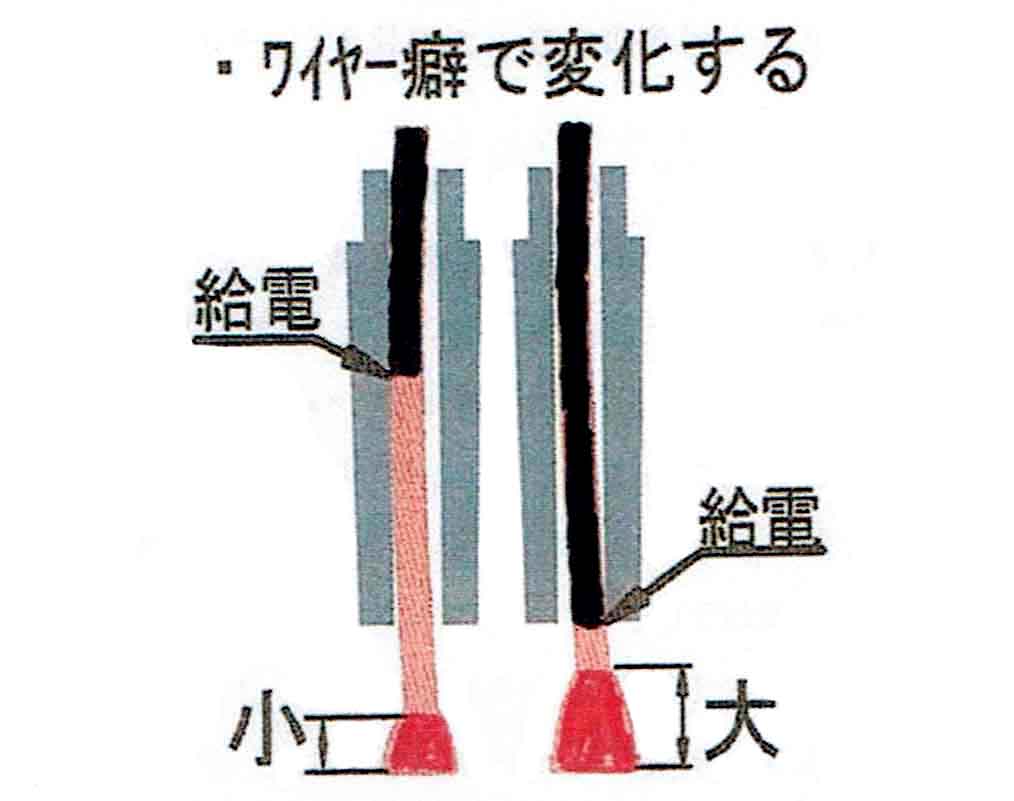
図3 従来型チップの給電状況
3.1 半割れ型チップの給電機構と構造
従来型チップの問題点を解決する方法として、図4に示すようなバネによる強制加圧給電方式の半割れ型給電チップを開発した。チップ台の中にあるチップ受台をバネで押すと、点Aで半割れチップの根本を下方に押すことになり、結果として、点Bを支点として回転モーメントが働いて、チップ先端の点Cでワイヤ中心方向に強制的にチップが押さえられ、ワイヤへの給電がスムーズに起こる。チップの溝内面が両チップで0.4mmまですり減っても給電が可能である。
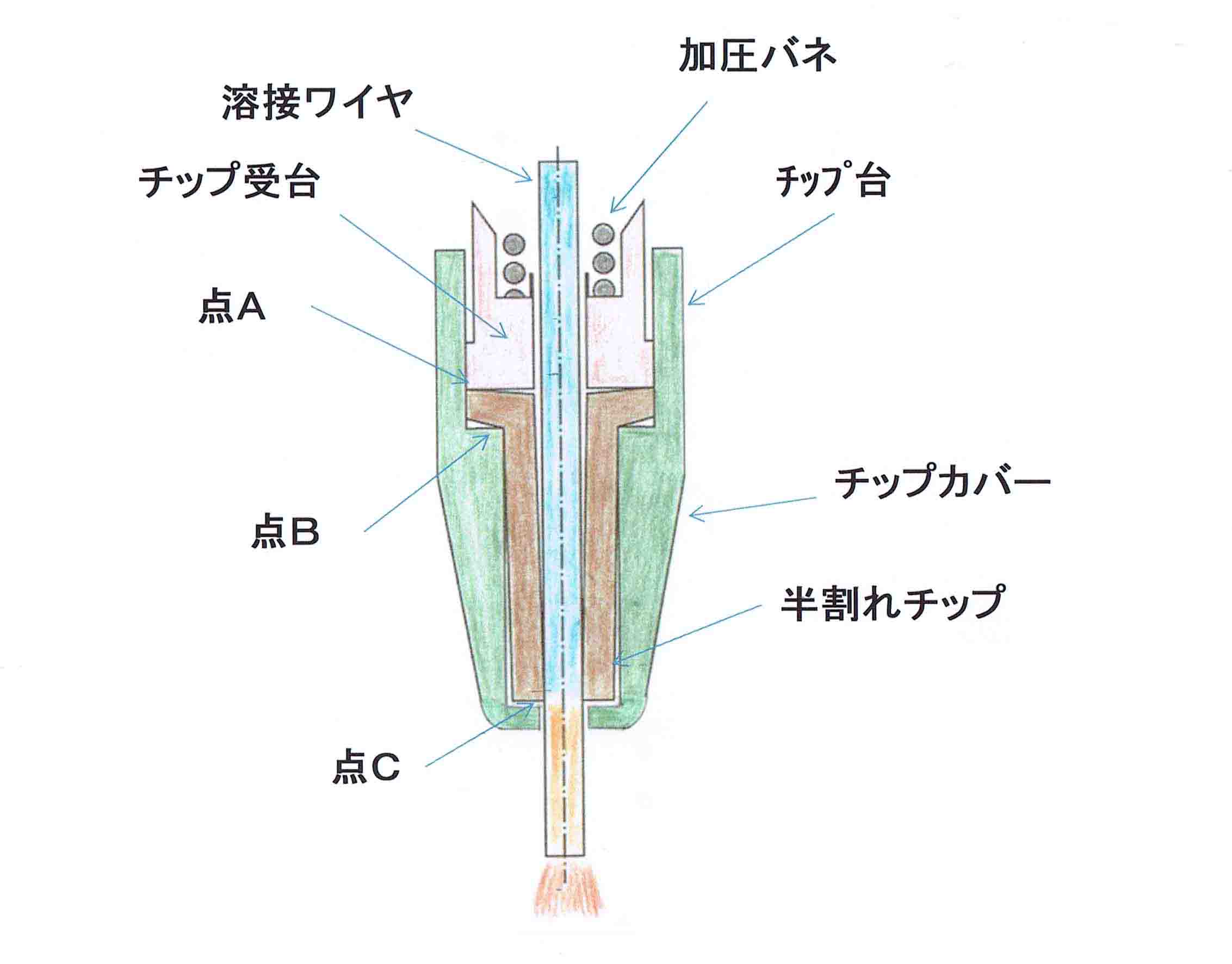
図4 半割れ型給電チップの構造
具体的には図5に示すように、現在利用されている溶接トーチに装着できるようにM6のネジを持つチップユニット(=チップ台+チップカバー+半割れチップ)として、図5のように製品化されている。 ここで、チップ台はほぼ1年間以上利用できるもので、チップカバーは1月に1,2本取り換えるものである。
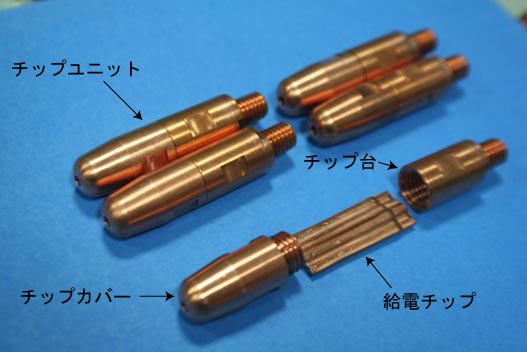
図5 半割れ型給電チップの構成
3.2 半割れ型給電チップの特性
(1) チップ給電位置とワイヤのジュール加熱
半割れ型給電チップの給電位置はチップ先端のみであり、その点からジュール発熱が生じる。チップ内部では溶接ワイヤの加熱は少ない。図6はこの状況を実際の溶接ワイヤの銅メッキの色の変化で示す。給電点はチップ先端であり、この点より右のチップ内部では銅メッキは変色していない。すなわち、500℃以上の高温にさらされていない。これに対して、チップ先端より左では給電しているのでジュール発熱が起こり、800℃以上に加熱され、銅メッキが黒色に変色している。このように、半割れ型給電チップはチップ先端の温度を500℃以下に保持できている。
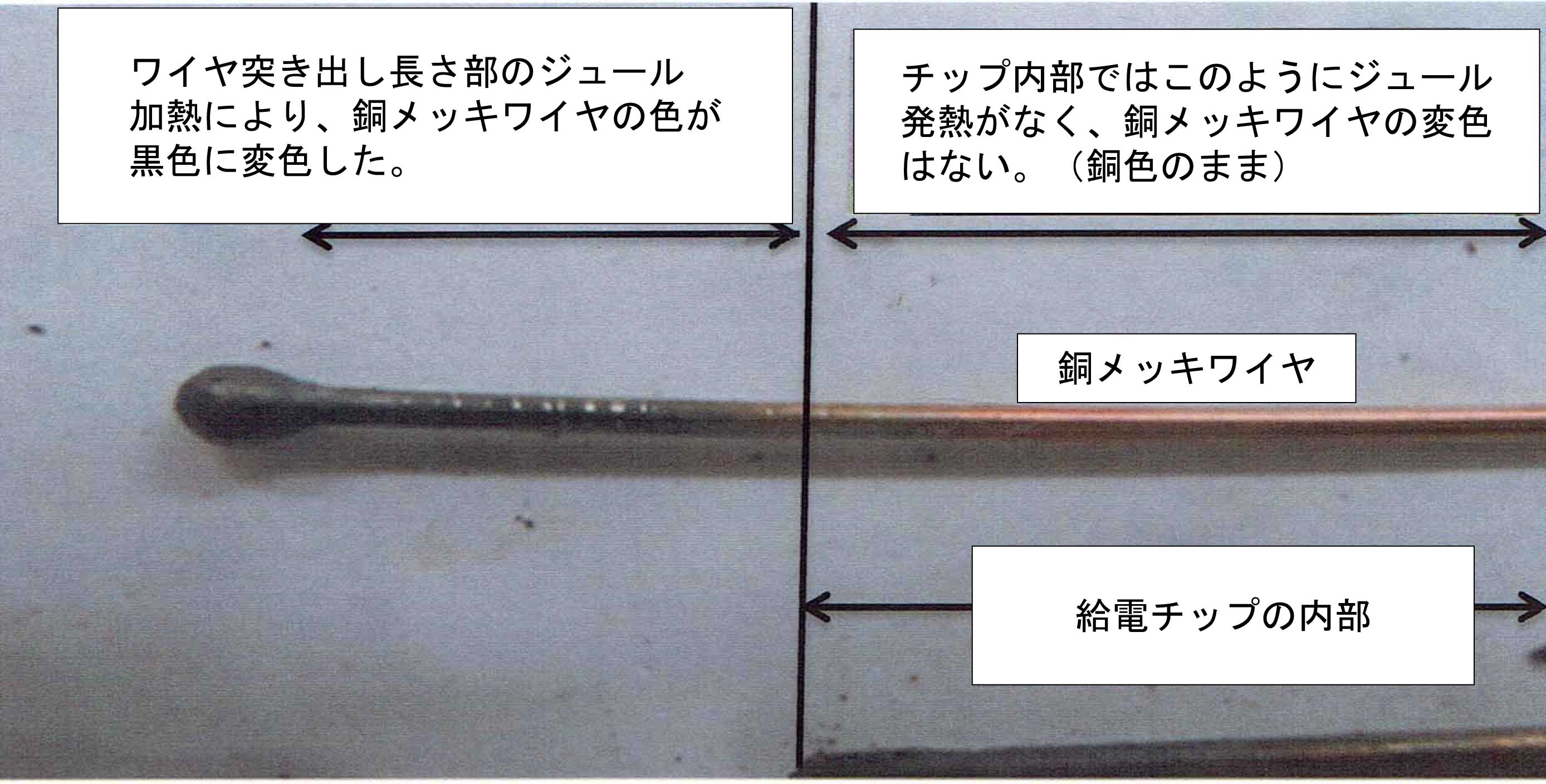
図6 溶接後の溶接ワイヤの色の変化領域
(2) チップ寿命
では、実際にチップの摩耗量は低減できるのか、実証実験で確認を行った。
1) 実験方法
ロボットおよびマグガス(80%Ar+20%CO2)を用いてMAG溶接を行った。半割れ型の給電チップを内蔵した給電チップユニットをトーチに取付けて、SS400鋼板(寸法:板厚9mm、200mmx600mm)上に、溶接ワイヤMG-50(1.2mm径)を用いてビードオン溶接した。1.8m長さの溶接ビードを3分間溶接した後、約2分休み、残り1.8m長さを3分間で溶接した。溶接条件は溶接電流を290A~310A、アーク電圧を約32.8V、溶接速度6600mm/minとした。36分毎にスパッタを除去した。その都度、ノズル内面にスパッタ防止剤を塗布した。いずれもアークタイム120分溶接した(溶接時間:4時間)後は、給電チップユニットを取り外し、チップの溝の深さをレーザ顕微鏡で計測した。図7はその溶接ビード外観を示す。スパッタの付着は少なかった。
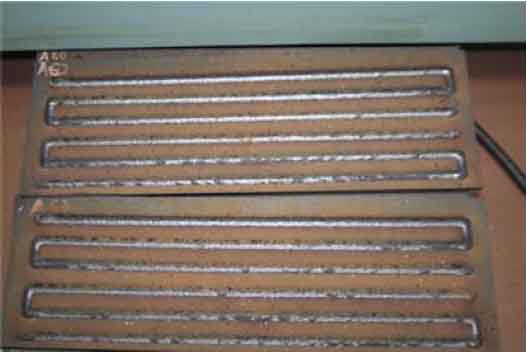
図7 溶接ビード外観
2) 実験結果
給電チップの溝内面の摩耗量をレーザ顕微鏡で計測した結果を図8に示す。この図より、従来型の一体型チップの摩耗量(250A,28V、1000mm/minの条件で、3%Cr銅チップを使用)が2時間で263μmであったのに対して、半割れチップの摩耗量は12時間で37μmとわずかであり、従来のチップと比較すると約39分の1であった。
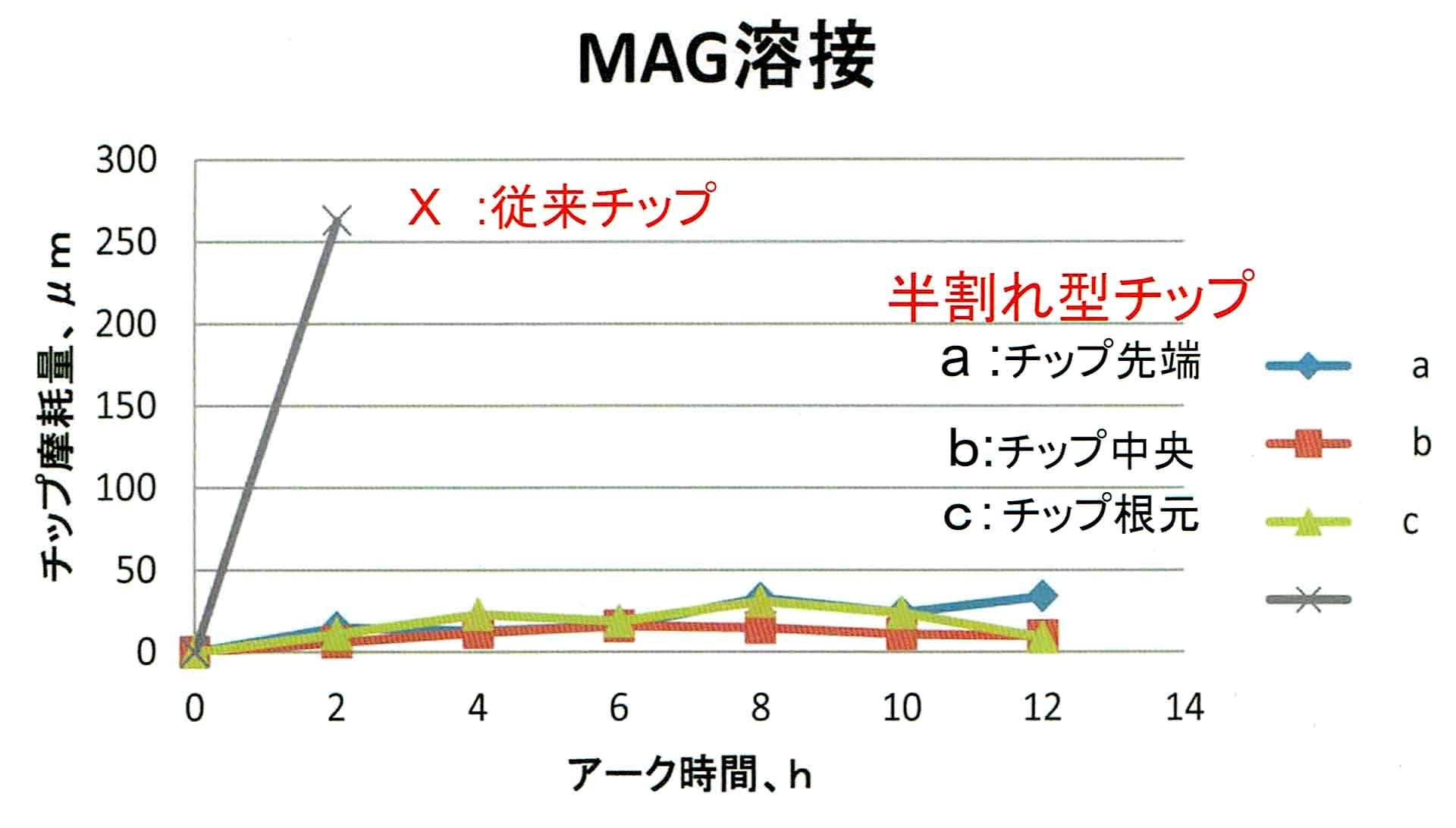
図8 半割れチップを用いたMAG溶接におけるチップ摩耗量の計測結果
(3) アーク安定性
給電点をチップ先端に固定できれば、ワイヤ突出し長さの変動が少なくなり、溶接電流およびアーク電圧が安定化する。そこで、半割れ型チップを用いた場合と従来チップを用いた場合の溶接電流の変動を計測し、図9に示す。このように、溶接電流の変動範囲が狭くなり、アークが安定していることがわかる。
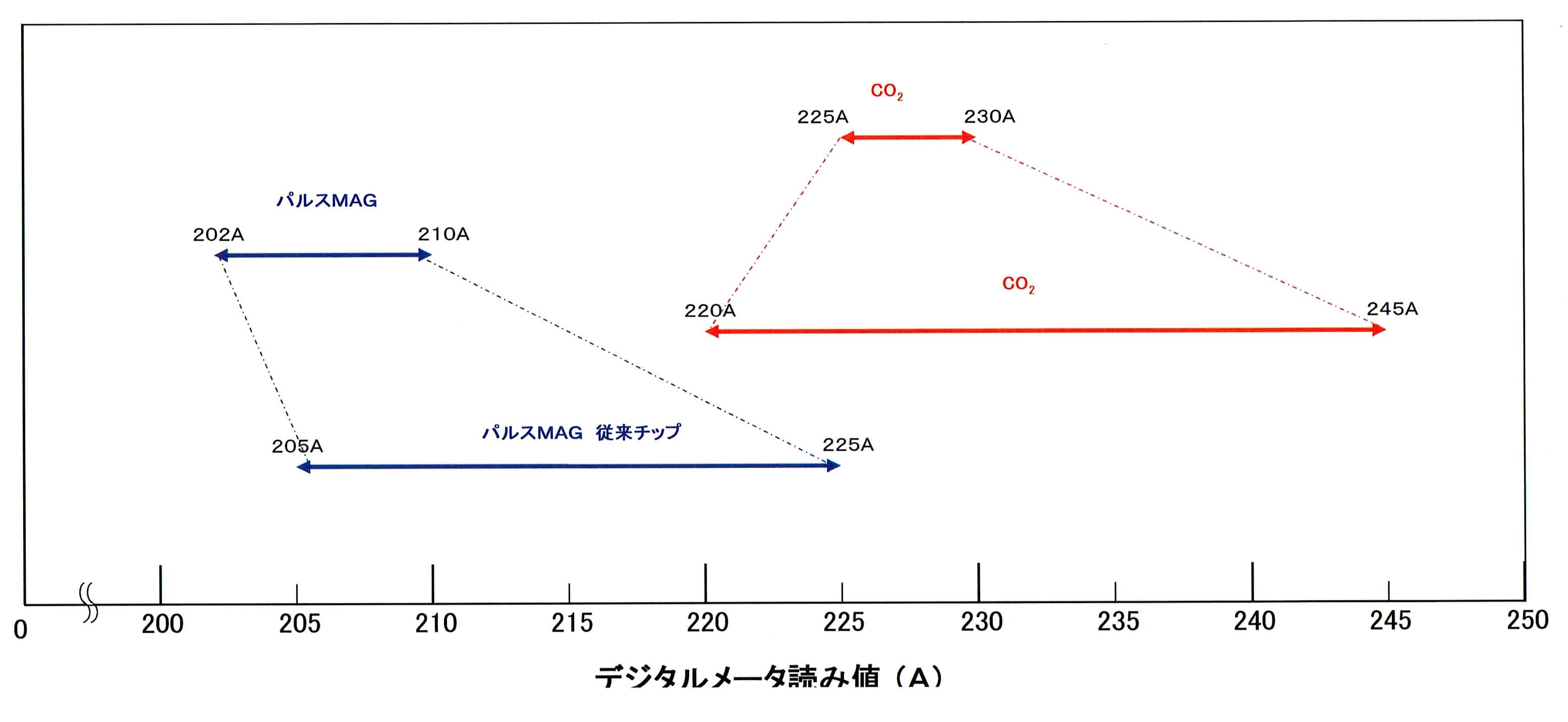
図9 半割れ型チップおよび従来型チップを用いた時の溶接電流の変動範囲
(4) スパッタの付着
チップ摩耗量の確証実験をアークタイムで12時間実施したときのノズルへのスパッタ付着量を計測した。その結果、CO2アーク溶接で0.137g/min、MAG溶接では0.0187g/minと微量であった。アークが安定していることからスパッタも少ないと言える。
購入方法
弊社および下記取扱店にて長寿命半割れ型チップの販売を行っております。
長寿命半割れ型給電チップ取扱店
株式会社ナ・デックス
株式会社マツモト産業
岩谷産業株式会社
豊田通商株式会社
扶桑産業株式会社
弊社より直接半割れ型チップをご購入の場合は、以下の見積依頼書に必要事項をご記入の上、FAX(0566-91-2282)もしくはE-mail(altrec-kutsuna@nifty.com)にてご連絡ください。
見積依頼書のダウウンロードはこちら
チップ形式と価格表
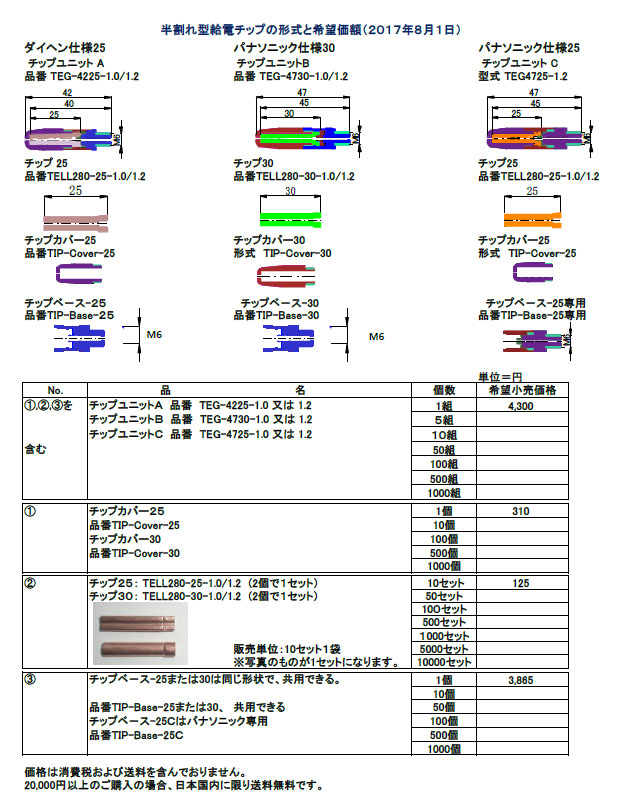